SOP’s & EOP’s
What are SOP's & EOP's?
SOP = Standard operating procedures.
A written instruction of how to operate the piece of equipment or system safely and within its operating limits under standard (normal) operating conditions.
Producing the Standard operating procedures (SOP) is part of the risk assessment exercise itself and provides a written means to instruct employees on how a particular procedure should be carried out and lays out boundaries of responsibility.
The process of writing a SOP necessitates thinking through all steps of a procedure and encourages the elimination of potential risks to the process itself. This is critical to providing reassurance and governance.
Operating procedures should clearly lay down instructions for operation of process plant that take into consideration COSHH, manual handling, permit to work, PPE Regulations, quality, HAZOP, and SHE requirements.
A common example within the boiler house would be how to undertake a gauge glass blowdown.
EOP = Emergency Operating procedure
Procedures for staff, or other trained & competent personnel to follow in an emergency.
The template falls much the same as the SOPs, however the risks now can vary quite significantly, and thus dynamic risk assessments must be undertaken when attending such an event.
A common example within the boiler house would be attending a boiler low level alarm condition.
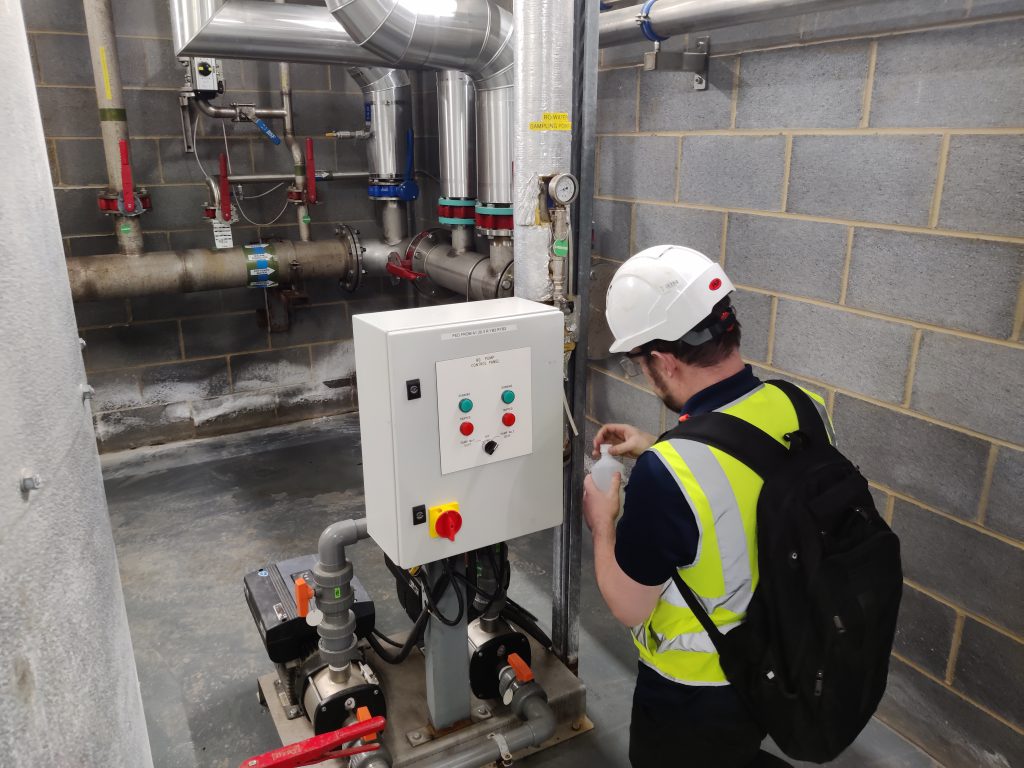
Why Provide SOP's & EOP's?
These documents in essence, provide guidance on the step-by-step explanation / instructions on how to conduct specific tasks and/or interact with equipment or systems. By setting out the way a certain task or activity can be undertaken safely, we aim to mitigate mistakes (either in action or timing) that could lead to situations where the safe operating envelope may be breached are averted.
It can be used to satisfy legal compliance requirements too.
The three key reasons for managing health and safety in an organisation and providing such SOPs & EOPs are
LEGAL REASONS
Providing adequate and suitable instructions for the operation of a systems is required by law.
Health and Safety Authority inspectors visiting workplaces will want to know how employers are managing safety and health. If they investigate an accident, they will scrutinise the risk assessment and safety statement, and the procedures and work practices in use. Make sure that these stand up to examination.
FINANCIAL REASONS
There is considerable evidence, borne out by companies’ practical experiences, that effective safety and health management in the workplace contributes to business success. Accidents and ill-health inflict significant costs, often hidden and underestimated.
No only this but the effective and efficient operation of plant can be found to save significant figures. A great example of this is the excessive operation of the bottom blowdown mounted to steam boilers.
MORAL AND ETHICAL REASONS
The process of writing a SOP necessitates thinking through all steps of a procedure and encourages the elimination of potential risks to the process itself. Employers are ethically bound to do all they can to ensure that your employees do not suffer illness, a serious accident or death.
What Procedures are Provided?
Whilst our procedures will be tailored specifically to your boiler house, below is an example list of procedures we will aim to produce.
SOP's
- Safe Entry Into The Boiler House
- Daily Checks
- Gauge Glass Procedure
- Automatic Bottom Blowdown Override Test
- Boiler TDS Sample
- Inspecting The TDS Probe
- Calibrating The TDS Probe
- Boiler Flame Failure Test
- Boiler Evaporation Test
- High Water Level Test
- Pre-Requisite Checks for Boiler Start-Ups
- Cold Start Up
- Warm Start Up
- Letting Steam Onto The Range – System Offline
- Isolating the boiler from the header
- Conservation When The Boiler Is Out Of Service
- Shutting Down A Boiler Fully
- Draining The Boiler
- Isolating The Fuel Supply – Gas
- Draining Down The Hotwell
- Adding Salt To The Brine Tank
- Adding Chemicals To The Tanks
- Log Keeping
- Defect Log
- Boiler House Security
EOP's
- Boiler Alarm Response
- Boiler Critical Alarm –
Plant Emergency Shutdown Pressure - Boiler Critical Alarm – Low Water Level
- Boiler Alarm – High Water Level
- Boiler Alarm – High Pressure
- Burner Lockout
- Loss Of Fuel Supply – Gas
- Fire
- Mains Power Failure
- Water Leak – Flood
- Steam Leak
- Boiler High TDS Alarm
- Chemical Spill
- Evacuation
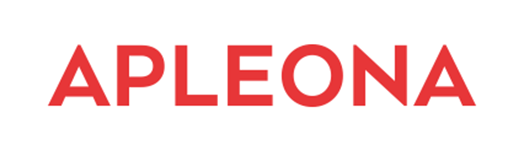
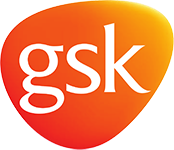
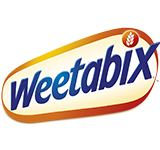
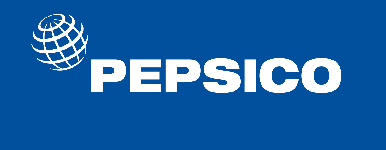
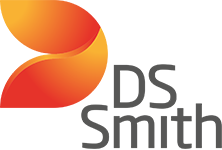


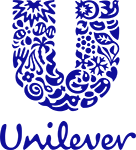
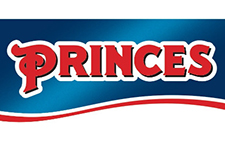
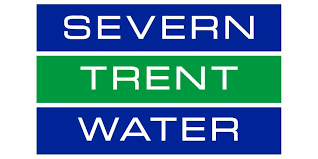
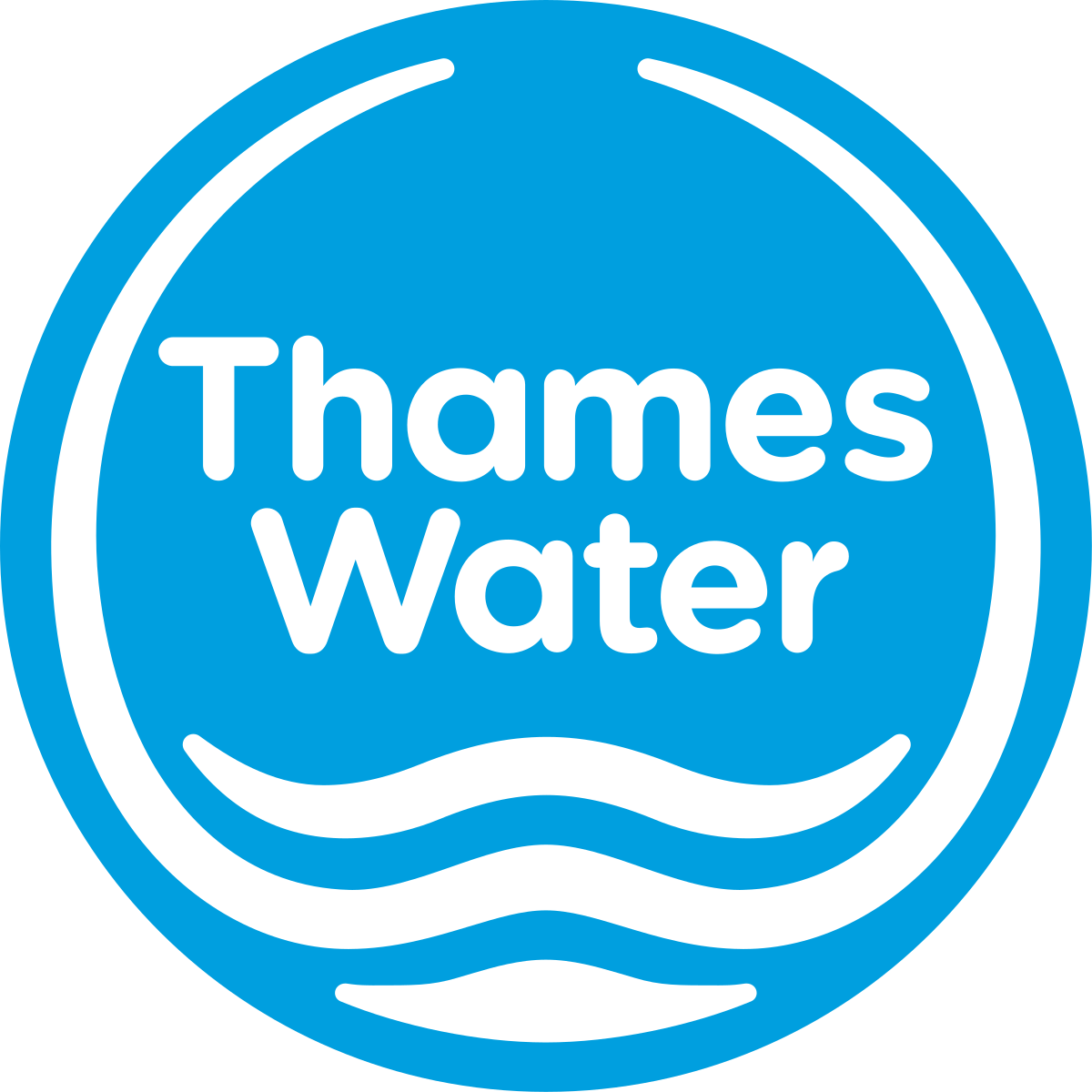